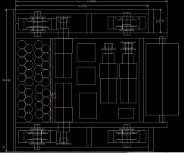 |
After designing and redesigning Helios, settling on a design, and aquiring most of the interesting parts, we started machining
the various frame pieces. This is a fairly early CAD of Helios. |
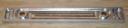 |
In order to save weight, we removed any uneeded material. A chain path is cut
into this particular piece. You can also see the brass bushings pressed into the piece. |
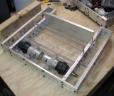 |
Here the frame is bolted together, and the drive motors are test fit. The 24V drill motors coupled
directly to the rear axle, and the front wheels would be chain driven from the rear.
|
 |
The drum was made out of aluminum pipe that our friend Derek Zahn had donated to the cause. We machined
end caps, and attached some heat treatable steel as teeth.
|
 |
The drum weight around 5 pounds, and was driven by a modified Jensen from TeamDelta. |
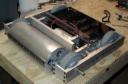 |
We used a few 1/2" drills as temporary axles to get a good idea of what the bot would look like.
|
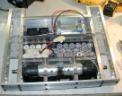 |
Everything is test fit. We made sure we didn't have a lot of wasted space in the bot. |
 |
We bolted most of the internal components to the 1/4" black polycarbonate base plate. Here are the
Victors going in. |
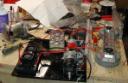 |
The frame was assembled and dissassembled many times just mounting all the components. |
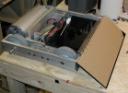 |
We had just enough weight in the budget to put a small rear wedge on. At least if our drum failed,
we could wedge someone to death! |
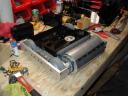 |
We used a ball caster from McMaster to ensure the bot was invertable. You can also see the timing belt
and pully used to drive the drum. |
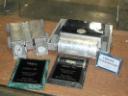 |
Helios ended up taking first place at HSRC02, and also was voted "Coolest Featherweight" by the competitors! |